Like most people who enjoy more cortisol than what comes with being a fan of the New York Football Giants, you decide to also play fantasy football. And if you really want to lose it, you play not only a redraft-style but a dynasty-style fantasy league. Naturally my buddies and I, all Giants fans (except one weirdo), did exactly that! 8-man 5-year dynasty league.
We call it The 5 Year Plan.
We decided a portion of our yearly dues will feed a mutual fund, growing (barring WWIII) to reward the team with the most Points For after the 5 years come to an end.
In order to keep track of performances I connected to Sleeper's API so that every Tuesday at 5 AM ET, the leaderboards update and rank the teams by most Points For. Points Against and Record (W-L) are included but not ranked. Fun project that provided me with experience in establishing a Google Cloud Service Account, integrating with Sleeper API and managing Google Sheets with Python, and embedding a published CSV leaderboard in HTML, all secured with JSON credentials.
Master's Capstone Project
Machine Vision Robotic Tool Grinder
My graduate research focused on developing a robotic tool grinder work cell using machine vision. The project integrated a CRB 15000 ABB Collaborative Robot, leveraging ABB's Force Control in RAPID programming. Additionally, it incorporated an IS5100 Cognex Camera and a Compact Logix 5370 Allen Bradley PLC. The goal was to achieve a repeatable 45° chamfer grind on a rectangular aluminum tool edge.
This mobile work cell integrated advanced technologies for precision tool manufacturing. Machine vision training utilized pattern and fixture detection, to calculate angularity. A stringent criterion based on visual inspections of Passed and Rejected parts guaranteed quality control. Furthermore, statistical testing validated the system's reliability, offering a robust solution for enhancing efficiency and precision in tool manufacturing processes.
If you would like to read the final report of the project, click the link below and stay tuned for more blog posts about the project!

Senior Design Project
Medical Supplies Drone
In our Mechanical Analysis Design class, myself and 3 others elected to undertake the task of designing, assembling, and testing a fully functioning prototype for a medical supplies drone.
Following the rigorous DMADV Six Sigma Methodology, we methodically engineered the entire product from conception to presentation. Utilizing an Arduino UNO as our microcontroller, we ensured precise management of input/output control throughout the drone's operation.
One of our primary responsibilities involved performing accurate calculations to appropriately spec the necessary motors, battery, and ESCs (Electronic Speed Controllers) needed to achieve the desired flight capabilities. These calculations factored in considerations such as weight distribution and the desired trajectory of the drone, ensuring optimal performance.
Upon completion of the project, each member of our team received Green Belt certification, affirming our mastery of the Six Sigma methodology and our ability to deliver high-quality solutions through disciplined problem-solving and successful execution.
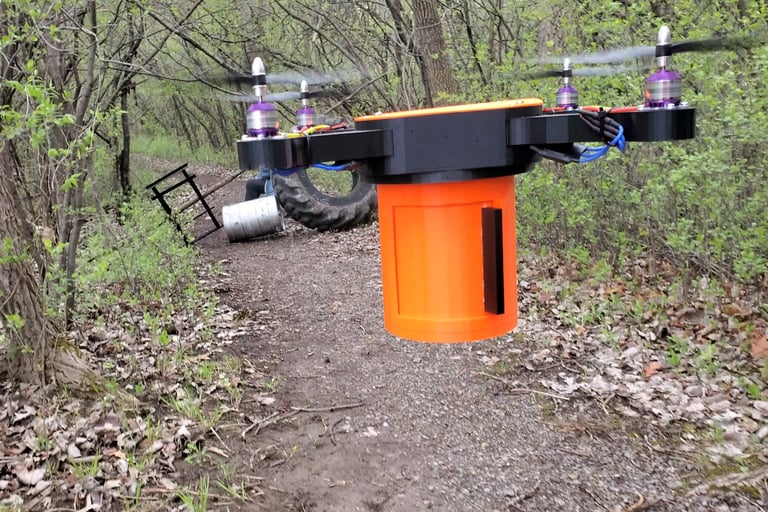
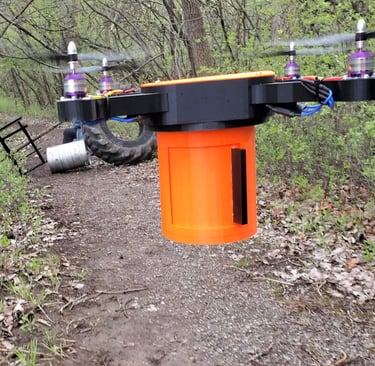
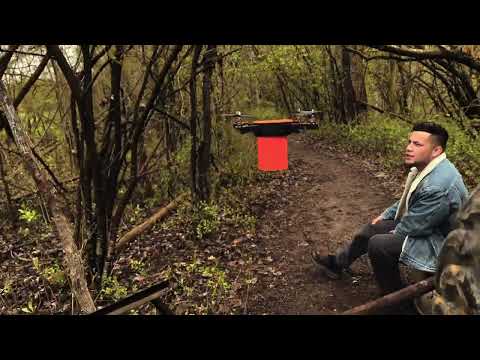
Machine Vision Robotic Dartboard Blaster
For our Robotics and Vision graduate course project, our team embarked on a semester-long endeavor to program an IRB 120 ABB robot to pneumatically fire a Nerf bullet at a dartboard.
Our project was multifaceted, requiring the integration of OpenCV to capture and post-process images from a standard webcam focused on the dartboard. Within the dartboard setup, three Aruco markers facilitated real-time adjustments, compensating for any shifts in the board's position, be it vertically or horizontally.
Additionally, TCP/IP (Transmission Control Protocol/Internet Protocol) played a crucial role in enabling seamless communication between the Python script and the RobotStudio virtual environment. This allowed our team to input desired parameters, such as the target pie slice (dartboard positions 1-20) and the desired multiplier (1x, 2x, or 3x), regardless of the dartboard's position. Using the photo taken and the identified location via Aruco markers, positional data was transmitted to the robot, ensuring precise alignment for an accurate shot.
Graded on our ability to land the dart accurately on a randomly generated number between 1 and 60, our team's success underscored our proficiency in leveraging advanced technologies to tackle real-world challenges in robotics and vision applications.
Robotic Vision Project
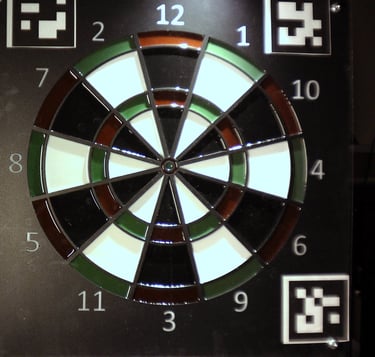
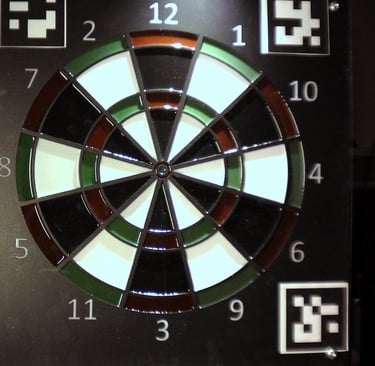
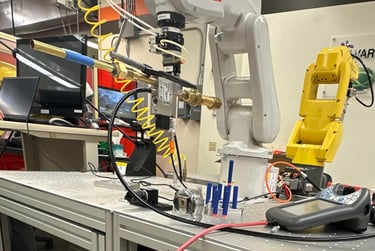
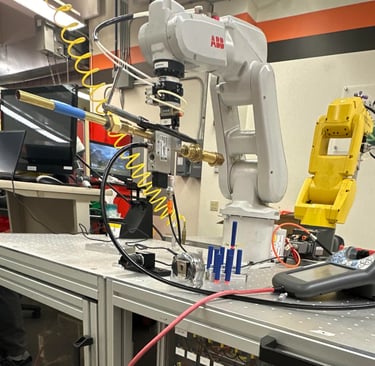
Aerodynamics Project
F-14 Variable Wing Sweep Aerodynamics
In our Aerodynamics Course, our team elected to assess and analyze the aerodynamic behavior of the variable wing sweep capability that an F-14 Tomcat possess under varying flight conditions.
The F-14's unique variable wing sweep feature was tested in both tucked and fully extended positions, with angles of attack ranging from 0 to 15 degrees. Using ANSYS Fluent, SolidWorks and 3D printed models, we compared lift forces under consistent airspeed. The experiment aimed to validate the CFD (computational fluid dynamics) results against yielded data from the FLOTEK® 1440 wind tunnel, as well as hand calculations. Pressure probes were placed along the top and bottom of the the wings and outer body of the modeled jet, capturing data for direct comparison. This comprehensive analysis sheds light on the accuracy of flow simulations in predicting aerodynamic performance being crucial for aerospace design and innovation.
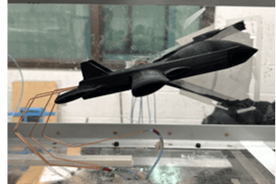
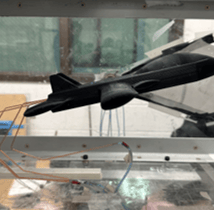
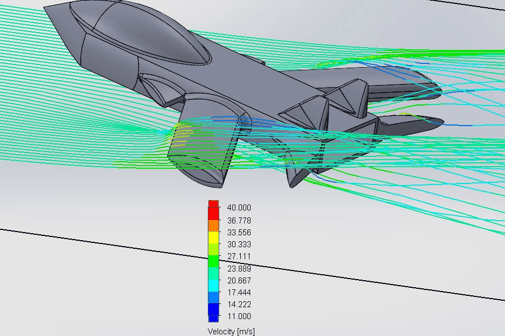
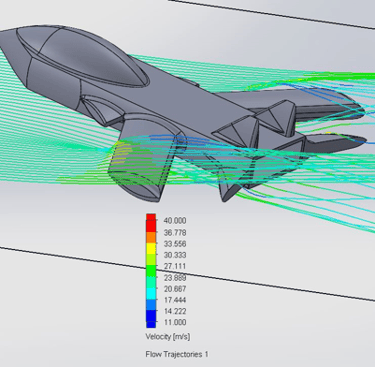
Fire Fighting Robot
In our Fluid Mechanics course, we utilized principles of fluid dynamics to design and simulate a robotic system for rapid deployment from a fire truck, adhering to specific constraints.
Through detailed calculations and simulations, motors, accumulators, and other components were precisely selected to ensure the desired performance will be achieved. While the robot itself was not physically built, it was fully modeled, paving the way for seamless integration into real-world applications. This project exemplified our ability to apply theoretical knowledge to practical engineering challenges with precision and efficacy.
Fluid Mechanics Project
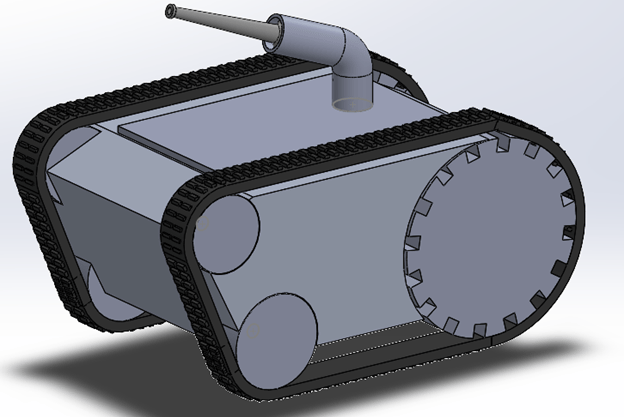
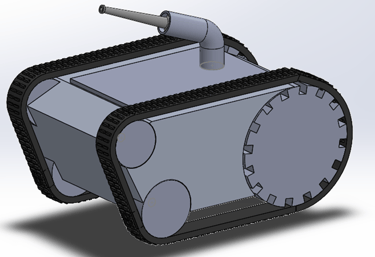